Defeitos em rolamentos de aerogeradores
- Marcos Nishioka
- 27 de fev. de 2023
- 7 min de leitura

Por que monitorar vibrações nos rolamentos de uma turbina eólica?
Dada a grande expansão de instalações de turbinas eólicas no Brasil e no mundo, desafios para com a operação e manutenção (O&M) desses ativos são cada dia maiores. Os parques possuem centenas de aerogeradores, a logística de peças é complexa, seu custo de aquisição é elevado e a indisponibilidade das turbinas é um problema recorrente. Com tais empecilhos, rotinas e sistemas que auxiliem nos processos de O&M são essenciais.
Nesse contexto, um dos principais elementos responsáveis por permitir o funcionamento de praticamente todas as turbinas eólicas são os rolamentos presentes em toda a extensão do drivetrain. Os principais responsáveis por fornecer livre movimento aos diversos eixos presentes no aerogerador. No entanto, estes não estão imunes a falhas que acontecem durante sua operação, as quais afetam diretamente sua vida útil, e consequentemente, a da sua respectiva turbina.
Por isso, o monitoramento de vibrações desses componentes é fundamental para garantir a sua correta condição de funcionamento. A tecnologia possibilita o diagnóstico precoce de defeitos nos rolamentos, pois permite a identificação de características vibratórias anormais. Dessa forma, os técnicos podem identificar defeitos prematuros, permitindo que as manutenções sejam realizadas a tempo de evitar a indisponibilidade dos equipamentos.
Aliando a identificação de ruídos de funcionamento anormal, vibrações excessivas, temperaturas elevadas, análise da lubrificação, entre outras variáveis, o diagnóstico e reparo de defeitos nos rolamentos é realizado de maneira muito mais inteligente, permitindo, portanto, que as manutenções sejam realizadas de forma eficiente.
Assim, o monitoramento vibracional dos rolamentos em turbinas eólicas é uma ferramenta essencial para manter a eficiência dos equipamentos e garantir a segurança dos processos de O&M. Esse artigo tem como principal objetivo discorrer sobre os rolamentos no contexto de aerogeradores e como fazer seu diagnóstico por meio de sistemas de monitoramento de vibrações.
O que é um rolamento e qual a sua função?
Rolamentos são tipos de mancais de máquinas rotativas, ou seja, são aparatos mecânicos que têm por intuito fazer com que um eixo possa girar com o menor atrito possível.
Podem servir também como anteparo de eixos com cargas axiais, como em pares de engrenagens helicoidais;
Mancais de rolamento são mais eficientes na sua função do que mancais de deslizamento.
Isso se dá porque o atrito viscoso dos mancais de deslizamento dissipa mais energia do que o atrito das interfaces do rolamento.
Rolamentos possuem diversos tamanhos e formatos, mas alguns de seus componentes são comuns. Eles são, conforme a figura:
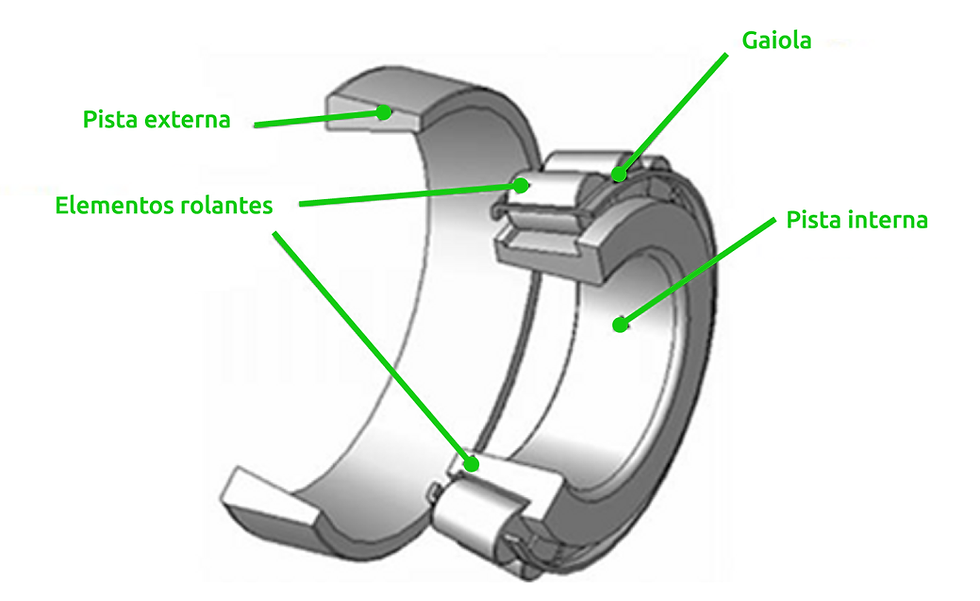
Pista interna;
Pista externa;
Elementos rolantes;
Gaiola.
Um detalhe importante sobre o funcionamento e o projeto de mancais de rolamento diz respeito a qual pista é girante, se a interna ou a externa. Dependendo da aplicação, faz mais sentido uma aplicação ou a outra.
QUIZ: Numa gearbox de aerogerador com 1 estágio planetário e 2 estágios paralelos, apenas um dos seus rolamentos tem projeto de pista externa girante e interna fixa. Qual é ele?
Quais os defeitos que um rolamento pode apresentar?
Defeitos em mancais de rolamentos em sua grande maioria são causados por 4 principais motivos/origens de falha:
Lubrificação inadequada;
Problemas com a pré-carga do rolamento;
Erros de fabricação;
Fadiga.
Contudo, apesar de origens distintas, a detecção de seus defeitos a partir de suas características vibratórias seguem padrões muitíssimo similares.
Como diagnosticar defeitos em rolamentos?
Para o caso de mancais de rolamentos e falhas em sua estrutura, há alguns aspectos bastante importantes sobre a dinâmica dos seus componentes. Há 4 frequências de interesse que acontecem a partir da frequência de rotação à qual o mancal de rolamento é submetido:
BPFO (Ball Pass Frequency on Outter race) - frequência de passagem de cada elemento rolante sobre um ponto fixo da pista externa;
BPFI (Ball Pass Frequency on Inner race) - frequência de passagem de cada elemento rolante sobre um ponto fixo da pista interna;
BSF (Ball Spin Frequency) - frequência de rotação de cada elemento rolante sobre seu próprio eixo;
FTF (Fundamental Train Frequency) - frequência de translação dos elementos rolantes, a qual é também a frequência de rotação da gaiola. * Essa é a única frequência que depende de como o rolamento é configurado (se é sua pista interna ou externa que é fixa). *
O cálculo dessas frequências pode ser realizado a partir das seguintes relações:

Onde m é calculado a partir de:

Obs: β é o ângulo de toque dos elementos rolantes sobre as pistas -> presente quando os rolamentos são elementos rolantes cônicos ou de pistas duplas.
Diferentemente das falhas em engrenagens ou componentes maiores associados aos mancais de rolamento, os defeitos nos rolamentos apresentam uma atuação muito pequena no espectro de frequência para com sua amplitude RMS.
Em outras palavras, normalmente quando há um defeito se desenvolvendo num mancal de rolamento, ele não altera significativamente o valor global do sinal, especialmente em seus estágios iniciais; Sendo assim, precisa-se definir outras métricas para se diagnosticar a presença de um defeito num rolamento.
Fator de Crista (FC)
Definido como a razão entre o valor de pico com o valor RMS do sinal aquisitado:

A lógica seguida pelo FC é a de que, quando um sinal de vibração possui um valor de pico muito maior do que seu valor RMS, isso se dá pela presença de imperfeições pontuais na estrutura do rolamento, fazendo com que toda vez que um elemento rolante passa por cima de alguma dessas imperfeições, ele causa esse aumento abrupto no valor de vibração.
Portanto, além dos valores globais de vibração, monitora-se esse parâmetro geral, a fim de detectar possíveis defeitos em mancais de rolamento em diversas partes do drivetrain.
Fator de Defeito (DEF)
Seguindo a mesma lógica do FC, o fator de defeito é bastante útil para a mesma funcionalidade de detectar possíveis falhas em mancais de rolamento. Ele é definido não pela razão, mas pela diferença entre o valor de pico e o valor RMS do sinal:

Como se trata de um valor absoluto com unidade de medida definida (a mesma da vibração aquisitada, nesse caso, g), o fator de defeito complementa o fator de crista ao fornecer um valor que leva em consideração a magnitude do valor global. A junção de ambas as métricas é bastante útil ao se realizar o ajuste fino de parâmetros de alarme e alerta dos sistemas de vibração.
Fator K (FK)
Por fim, o fator K é definido como o produto entre o valor de pico e o valor RMS:

A filosofia de diagnóstico é a mesma utilizada para os dois parâmetros anteriores. A principal vantagem do fator K é que ele, diferente dos anteriores, é sempre progressivo e apenas aumenta conforme a falha no rolamento se desenvolve.

Modulação
Modulação é a palavra chave para definir como atua uma falha em um rolamento. Conforme um defeito aparece em algum dos componentes do mancal, o que ocorre é que tal defeito serve como um pulso vibratório, uma pancada.
Essa pancada, por si só, age como um delta de Dirac sobre o sistema (excitando, teoricamente, todas as frequências dele), revelando as frequências naturais desse mancal de rolamento em específico. Porém, por ser apenas um pulso (com relação à sua aplicação no tempo), pelas características dissipativas de todos os materiais e pela alta frequência natural de materiais metálicos, esse sinal vibratório possui curtíssima duração. Contudo, esse pulso não acontece apenas uma vez, visto que os elementos rolantes estão o tempo todo fazendo esse pulso se repetir pela sua passagem sobre o defeito.

Descobrir qual é essa frequência de repetição dos pulsos é a grande tarefa do diagnóstico de defeitos em mancais de rolamento. Essa frequência de repetição de pulsos indica onde se localiza a falha: se está na pista interna, externa, num elemento rolante ou na gaiola.
Assim, o processo de demodulação do sinal é a melhor maneira de se isolar as frequências moduladoras (que localizam o defeito) e suas portadoras (naturais do rolamento). Utiliza-se, para esse fim, o processo de envelope por meio da transformada de Hilbert.
Por fim, há algumas nuances que ocorrem conforme a falha se desenvolve, formando "fases":
Fase 1:
Falha muito incipiente. Defeito macroscópico e localizado, porém pouco ou nada preocupante;
Aumento dos parâmetros de detecção de problemas em rolamentos (FC, DEF e FK);
Detecção de frequências de rolamento (BPFI, BPFO, BSF ou FTF, dependendo de onde a falha está localizada na estrutura do rolamento) no espectro envelopado;
Vários meses de antecipação para que se realize troca do componente;
Recomendação: manter monitoramento.
Fase 2:
Falha pouco grave. Leve evolução da condição anterior;
Aumento dos parâmetros de detecção de problemas em rolamentos;
Aumento de frequências de rolamento no espectro envelopado;
Possível detecção de frequências de rolamento no espectro puro de frequência;
Aumento quase imperceptível dos valores globais de vibração;
Meses de antecipação para que se realize troca do componente;
Recomendação: Manter monitoramento. Se houver recurso, agendar boroscopia.
Fase 3:
Falha intermediária-grave. Grande evolução dos defeitos macroscópicos localizados e início de defeitos distribuídos;
Aumento dos parâmetros de detecção de problemas em rolamentos;
Aumento de frequências de rolamento no espectro envelopado e no espectro puro;
Detecção de frequências de rolamento no espectro puro de frequência;
Aumento perceptível dos valores globais de vibração;
Possível aumento de temperaturas;
Semanas de antecipação para que se realize troca do componente;
Recomendação: Executar boroscopia para confirmar falha. Agendar troca ou reparo do componente.
Fase 4:
Falha grave. Defeitos distribuídos e de grande magnitude;
Diminuição de FC e DEF e aumento de FK;
Característica aleatória nos espectros de frequência;
Forte aumento dos valores globais de vibração;
Aumento relevante de temperaturas;
Possível propagação de defeitos para outros componentes do drivetrain. Risco de falha catastrófica;
Dias de antecipação para que se realize a troca do componente. Risco de falha catastrófica;
Recomendação: Trocar componente imediatamente. Se possível, limitar ou executar parada total do aerogerador, evitando falhas catastróficas.
Conclusões:
É possível diagnosticar defeitos em mancais de rolamento a partir de análises de vibrações, com o uso de parâmetros como Fator de Crista, Fator de Defeito e Fator K, adicionando-os às rotinas de verificação de alarmes para as suas turbinas. Além disso, o processo de modulação dos sinais de vibração oferece a possibilidade de identificar a frequência de repetição dos pulsos, e localizar o defeito. Ademais, existem quatro fases que esses defeitos passam enquanto evoluem, que exigem medidas de manutenção diferentes, que vão desde monitoramento até troca ou manutenção do componente.
Os sistemas VibraOne-Wind instalados em aerogeradores, por sua vez, são capazes de realizar diversas dessas ações de forma automatizada e precisa. Por meio da interface OneBreeze, o usuário pode analisar a condição indivual de cada aerogerador da sua frota, e tomar a decisão pautada em dados sobre quais ações devem ser tomadas individualmente por aerogerador.

A AQTech, adicionalmente, fornece serviços que fazem a análise da condição dos ativos monitorados. Dessa forma, os insights aos clientes são fornecidos de forma imediata, tornando as decisões de manutenção mais rápidas e assertivas.
Comments